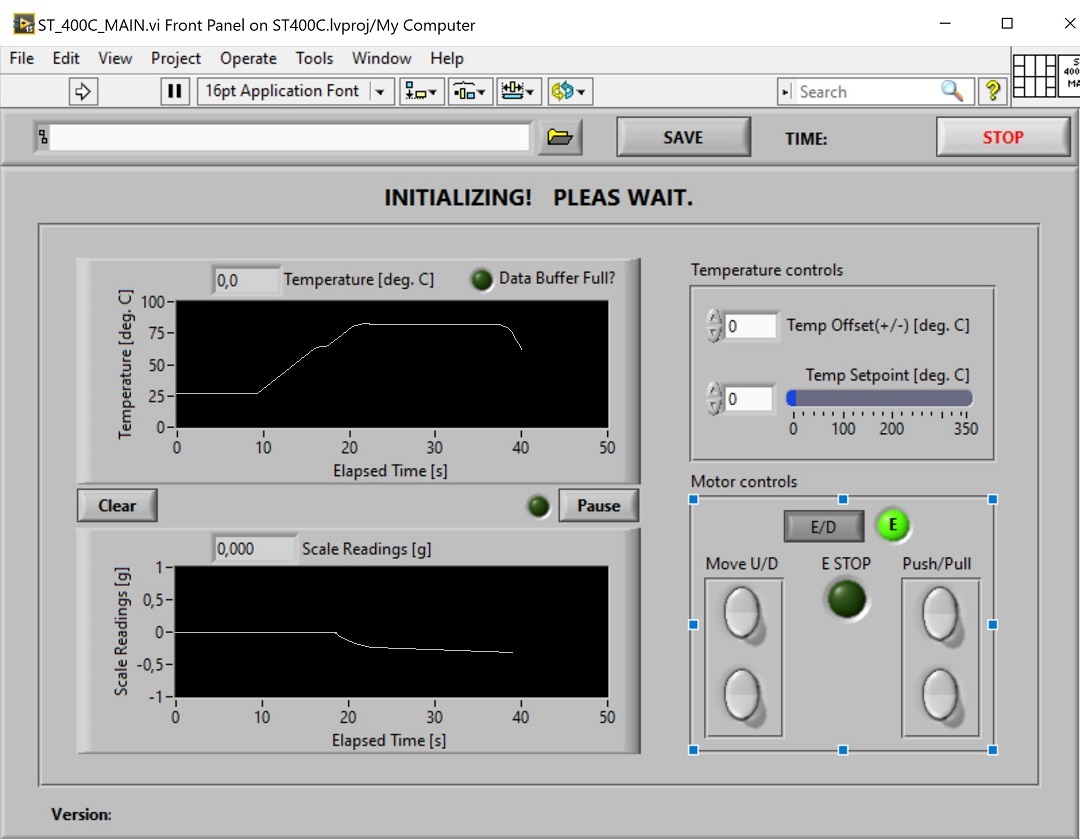
MyDAQ/MyRIO Temperature controller
Goal: Тhis project aims to development of precision Temperature controller for resistive type of loads (like typical heaters), programmatically controlled by standard NI MyDAQ/MyRIO boards.
Main features
- Fully open source. All schematics, wiring diagrams and LV2015 PDS source code are available.
- Designed for NI MyDAQ/MyRIO boards. All required IO signals are from the board, directly connected to 20 pin screwed terminal.
- Precision bridge measurement of the temperature. Currently software and the schematics are set up for PT100 temperature sensors, but with slight software and hardware modification all types of thermo-resistive sensors can be used.
- Heater current up to 2 [A] – higher current rates are also possible.
- Precise, full range (0 - 100%) control of the output power.
- High level software integration of PID algorithm for a temperature stabilization of +/- 0.5 [deg. C].
- Heating and cooling cycles programing.
- Automated data gathering.
Applications
Precision temperature control – a standalone version of the system, based on STM32 microcontrollers, was also developed for the purpose of temperature stabilization of optical BiBO Nonlinear crystal for second harmonic generation at 1340 [nm]. The crystal is placed in a specially designed oven connected to the thermoregulator. The oven mounted in a kinematic optical holder is shown in the picture below.
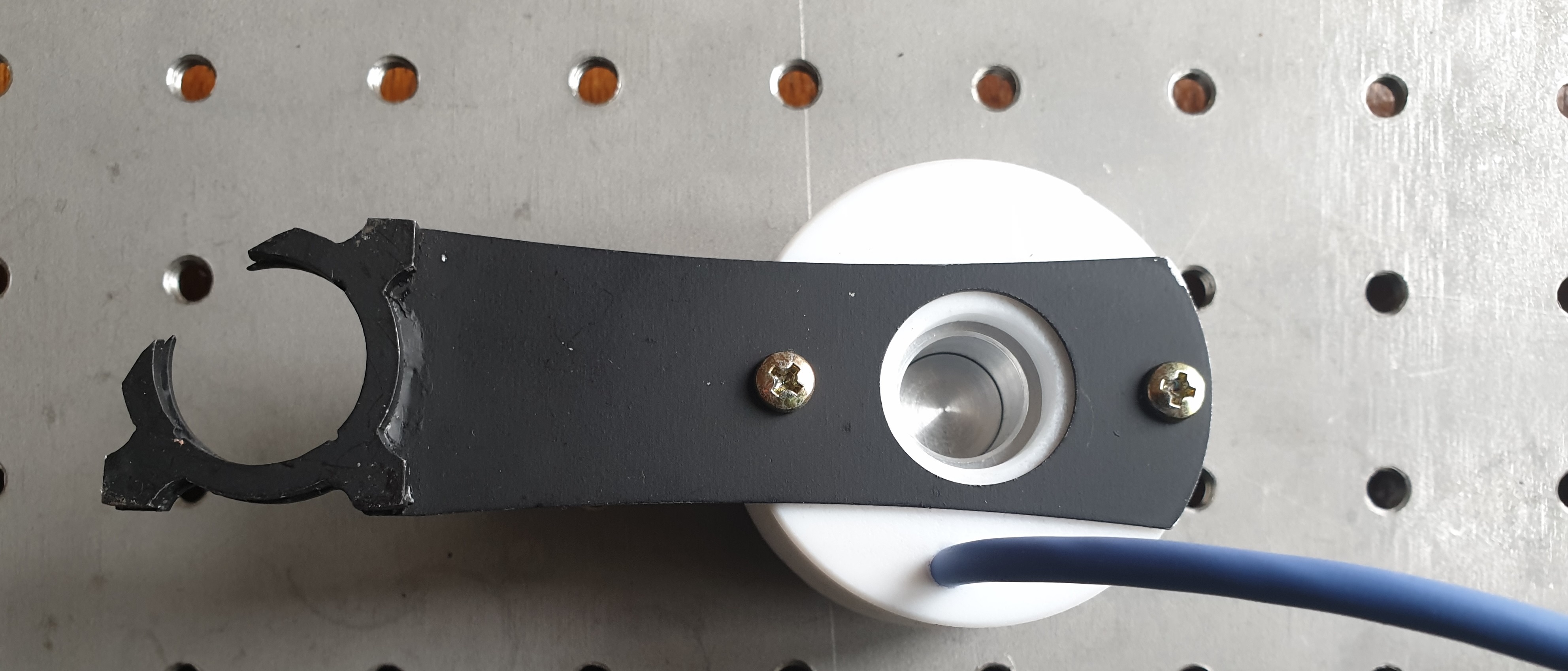
We use this system in one of our Nd: YVO4 picosecond laser systems. The picture below shows laser system operational I Mode Locking regime. The red light is coming from BiBO second harmonic generation crystal.
For the purpose of integration of the system within already existing setups, a high-level command protocol is available. All main function can be controlled by high level command using standard RS232 serial protocol. The system is also coming with a LabView 2015 example with a source code for fast starting and easy integration.
In case of interest to any of this applications or version of the system, do not hesitate to contact me and ask for more information.
Education - The system was originally designed for education. The idea was to build a hardware that can be controlled by standard NI boards and to use this hardware in our university LabView course. Students get only the HW and simple instruction to build a precision temperature controller.
The system is appropriate for all level of education. In the introductory level of LabView programming students use express VIs to establish connection with device, a designed simple On/Off temperature controller, gathering temperature data and plot them on a real time graph. For more advanced students the challenge is to use PID functions available in LabView setting up the PID coefficients for maximum performance (precision of temperature stabilization, fast reaching of the setpoint, no overshooting etc.). As a challenge they can use some more advanced algorithms like fussy logic and Kalman Filter to design their own algorithm for temperature control.
General purpose temperature control - The system was also integrated in one of ongoing projects, connected with the study of surface properties of liquid metals and low temperature alloys. We use the controller for heating a small amount of PbSn alloy up to 400 [deg. C] and stabilized the temperature at different setpoints. On the picture below you can see typical Heating-Cooling curve of the sample, with a setpoint of 325 [deg. C].
Later the system was integrated successfully within an apparatus for surface tension characterization. More information about this project can be found in the project page.